Login to continue reading
And access exclusive content, personalized recommendations, and career-boosting opportunities.
Don't have an account? Sign up
Blogs you need to hog!
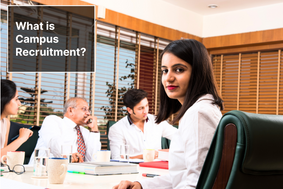
What is Campus Recruitment? How To Tap The Untapped Talent?
Shivangi Vatsal
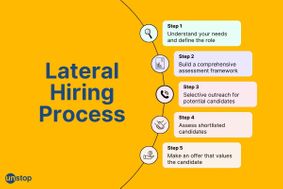
Lateral Hiring: A Complete Guide To The Process, Its Benefits, Challenges & Best Practices
Srishti Magan
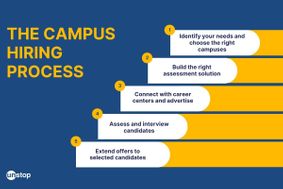
Step-By-Step Approach To Building A Winning Campus Recruitment Strategy
Srishti Magan
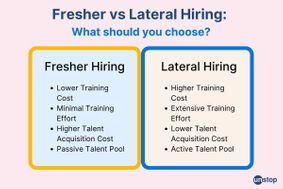
Lateral vs Fresher Hiring: Which Is A Better Choice?
Srishti Magan
Comments
Add comment